COOLED EGR
Up until 2004, manufacturers of diesel engines were able to comply with NOx emissions regulations without the use of EGR devices. Almost all highway diesels had some sort of EGR by the EPA model year 2004 (started in October 2002). EGR’s goal is to add “dead” gas, or gas that has already been used up and will eventually turn some of the cylinder volume inert, to the intake charge in order to dilute it. The goal is to minimize NOx emission by decreasing combustion heat, but engine OEMs have never been fond of the notion since it reduces engine power and fuel economy and introduces exhaust gas pollutants that are channeled back into the cylinders. Truck owners who had to pay for the EGR-related repairs to their vehicles were even less fond of it. The majority of engine OEMs have either completely abolished or maintained the EGR cut percentages to a minimal with the introduction of selective catalytic reduction (SCR) in EPA 2010 regulations. It makes sense to cool engine exhaust gas as much as possible before returning it to the engine’s cylinders. The majority of engine OEMs employ cooled exhaust gas recirculation because of this. sometimes referred to by the term C-EGR.
Components for C-EGR
Because the mixture percentage, sometimes referred to as the cut-percentage, changes depending on how the engine is operated, a typical C-EGR system on a diesel engine must be ECM controlled. Depending on the producer and the year of production, this might be anywhere between 0% and 50%. A C-EGR system typically includes:
- Heat transfer device (engine coolant is used)
- Mixing chamber controlled by ECM (mixes boosted air with exhaust gas to set cut-percentage)
- Airflow mass sensor
- Plumbing for the heat exchanger’s heat transfer of engine coolant
- Pipes that transport exhaust gases to the mixing chamber
We examine a few different diesel engine EGR system modifications, such as Caterpillar’s “clean” EGR system. Any engine that uses an EGR system benefits from C-EGR since it reduces the intake charge’s initial heat, which has the potential to increase NOx production. One OEM equips some of its medium-bore, work-related engines with an internal exhaust gas recirculation (I-EGR). A heat exchanger is not required with I-EGR. The engine is made to redirect part of the end gas back into the cylinder for the following cycle during valve overlap.
GAS INDUCTION OF CLEAN (CGI)
Without using EGR, Caterpillar was able to comply with the EPA’s 2004 highway diesel engine emissions regulations. However, Caterpillar decided to alter EGR in order to surpass 2007 EPA regulations. We previously described an EGR system’s goal as dilution of the intake charge with “dead” gas. Unreactive gas, often known as dead gas, enters the engine cylinder with the intention of doing nothing more than taking up volumetric space. Similar to decreasing the engine displacement in some operating modes The goal is to lower engine temperatures and, consequently, NOx emission. A high displacement engine will act like a smaller displacement engine as a result. The EGR concept requires a dead gas source to work correctly. The engine exhaust system, which produces dead gas whenever the engine is operating, is the best source of this gas, in actuality.
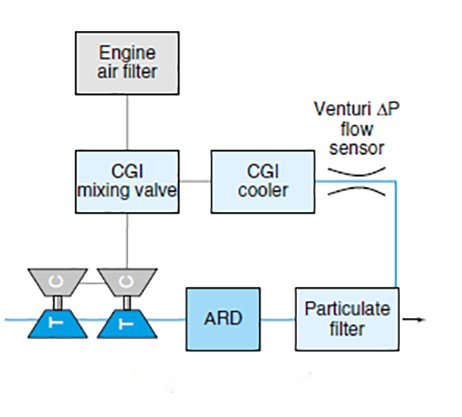
Caterpillar’s post-2007 ACERT series of engines employ clean gas induction (CGI), a kind of EGR. Because it gets its “dead” exhaust gas from a source downstream of the DPF, it varies from EGR. The Cat system is known as “clean EGR.” Similar to its competitors’ EGR, CGI is monitored by a mass airflow sensor (MAF), and the system goal is to maintain lower combustion temperatures to minimize under specific operating circumstances. The CGI pipe may be observed to exit the muffler/converter/DPF assembly near to its exit, making it simple to recognize a Cat CGI engine. This line connects the low pressure turbocharger to the intake circuit, returning the dead gas—which is supposedly clean—there.
The CGI gate is spring-loaded to default to no-recirculation when it comes to controlling CGI cycles. Up to 15% mixed concentration of gas from the clean side of the DPF is permitted (up to 50% with EGR systems). ECM management prevents CGI from happening during DPF regeneration cycles.
sensor CGI
Three sensors are used by a CGI system. The absolute pressure sensor and the pressure differential measurement sensor are two types of pressure sensors, while the temperature sensor is the third. After leaving the CGI venturi, the gas enters a bundle-style heat exchanger that uses coolant cooling. Similar to EGR engines, cooling recycled exhaust gas has a benefit. . A precooler will also be used by the heavy duty line of engines from Cat. A delta (three-terminal), variable capacitance type sensor is what the CGI pressure sensor uses. A linear proportioning solenoid, or pulse width modulated (PWM) actuator, powered by V-Bat voltages, regulates the CGI gate.